Graphite dies for continues casting of aluminium, copper
The process of continuous casting essentially is that of pouring molten metal into a graphite die, which is water-cooled. The metal then solidifies and is withdrawn from the die by means of take off rollers.
This process offers the advantage of non-stop production and also ensures optimum material quality.
When continuous casting with the die adjoining the melting chamber, two alternative procedures are possible:
- Casting with horizontal installation
- Casting with vertical installation
Advantaged of graphite are:
- Low surface wetting by molten metals
- High thermal and chemical resistance
- Increasing strength with a rise in temperature
- Good lubricating and frictional proper
- Excellent resistance to temperature change
- High thermal conductivity
Complicated parts with close tolerances can be machined into required shape.
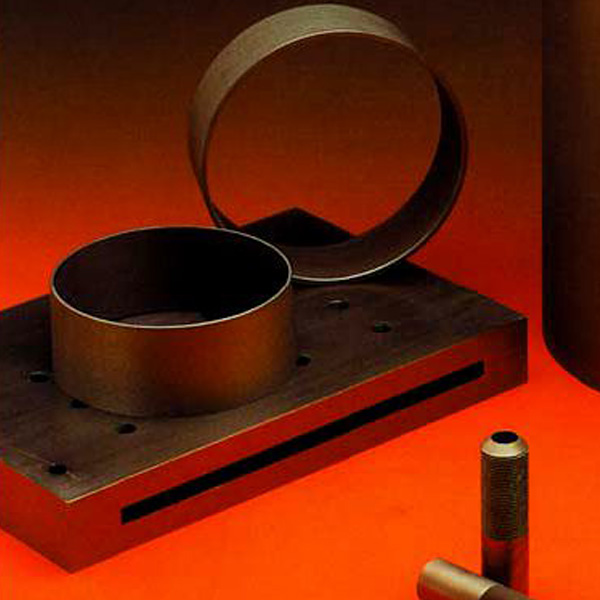
TOKAI CARBON’S GRADES FOR CONTINUES CASTING DIES
Grade | Specific Gravity (-) | Specific Resistance (μΩm) | Young’s Modulus (GPa) | Flexural Strength (MPa) | Shore Hardness (-) | *C.T.E (×10-6/°C) | Thermal Conductivity (W/mK) |
G330 | 1.79 | 13.0 | 9.8 | 39.2 | 53 | 4.8 | 104 |
G347 | 1.85 | 11.0 | 10.8 | 49.0 | 58 | 5.5 | 116 |
G348 | 1.92 | 10.0 | 12.3 | 63.7 | 68 | 5.5 | 128 |
G458 | 1.86 | 9.5 | 11.3 | 53.9 | 54 | 4.4 | 139 |